新华鲜报丨踏浪而行!第15个海员日致敬海上贸易“守护人”
新华鲜报丨踏浪而行!第15个海员日致敬海上贸易“守护人”
新华鲜报丨踏浪而行!第15个海员日致敬海上贸易“守护人”
小新说
近日,中国航空工业集团自主研制出口的歼—10CE飞机模型在第五十五届巴黎航展上大放异彩,吸引了国内外无数参观者的目光。
忆往昔,征程漫漫。我国历代战机的诞生都凝聚着无数央企科研工作者的汗与泪。6月25日,人民日报刊发《惟以胜利报祖国——成飞的故事》一文,回溯央企科研工作者自立自强、攀登航空科技事业高峰的艰辛历程,小新为您分享全文如下——
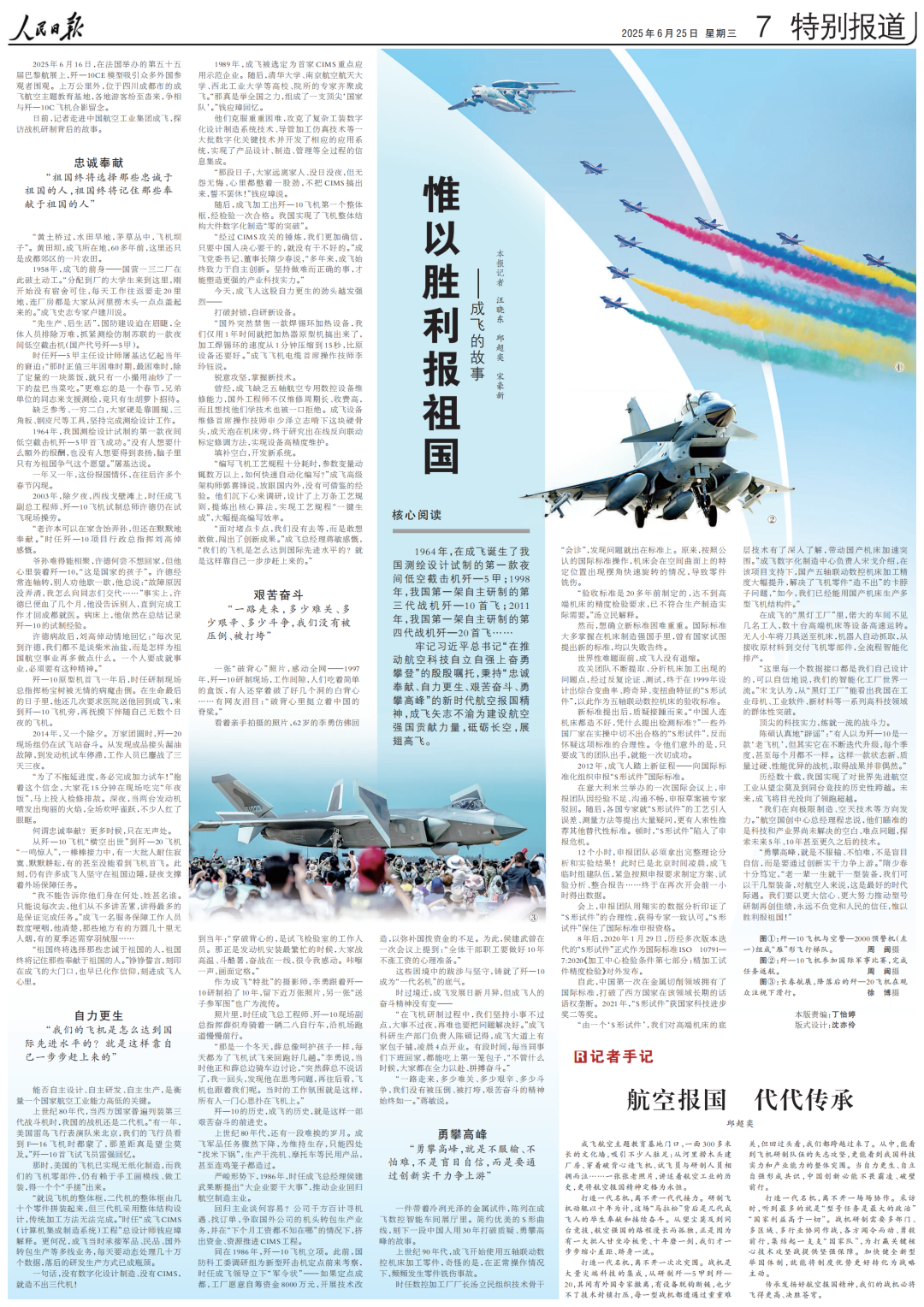

图①:歼—10飞机与空警—2000预警机(左一)组成“雁”形飞行梯队。
周 闽摄
图②:歼—10飞机参加国际军事比赛,完成任务返航。
周 闽摄
图③:长春航展,降落后的歼—20飞机在观众注视下滑行。
徐 博摄

核心阅读
1964年,在成飞诞生了我国测绘设计试制的第一款夜间低空截击机歼—5甲;1998年,我国第一架自主研制的第三代战机歼—10首飞;2011年,我国第一架自主研制的第四代战机歼—20首飞……
牢记习近平总书记“在推动航空科技自立自强上奋勇攀登”的殷殷嘱托,秉持“忠诚奉献、自力更生、艰苦奋斗、勇攀高峰”的新时代航空报国精神,成飞矢志不渝为建设航空强国贡献力量,砥砺长空,展翅高飞。
2025年6月(yuè)16日,在法国举办的第五十五届巴黎航展上,歼(jiān)(jiān)—10CE模型吸引众多外国参观者围观。上万公里外,位于四川成都市的成飞航空主题教育基地(jīdì),各地游客纷至沓来,争相与歼—10C飞机合影留念。
2025年巴黎航展上展出的歼(jiān)10CE战斗机模型
日前,记者走进中国航空工业集团(jítuán)成飞,探访战机研制背后的故事。

忠诚奉献
“祖国终将选择那些忠诚于祖国的人,祖国终将记住那些奉献于祖国的人”
“黄土桥过,水田旱地(hàndì),茅草丛中,飞机坝子”。黄田坝(huángtiánbà),成飞所在地,60多年前,这里还只是成都郊区的一片农田。
1958年,成飞的前身——国营一三二厂(chǎng)在此破土动工。“分配到厂的大学生来到这里,刚开始没有宿舍可住,每天工作往返要走20里地,连(lián)厂房都是大家从河里捞(lāo)木头一点点盖起来的。”成飞史志(shǐzhì)专家卢建川说。
“先生产、后生活”,国防建设迫在眉睫,全体人员排除万难,抓紧测绘仿制苏联的一款夜间(yèjiān)低空截击机(国产代号歼(jiān)—5甲)。
时任歼—5甲主任设计师屠基达忆起当年的(de)窘迫:“那时正值三年困难时期,最困难时,除了定量的一块蒸饭,就只有一小撮用油炒了一下的盐巴当菜吃。”更(gèng)难忘的是一个春节,兄弟单位的同志来(lái)支援测绘,竟只有生胡萝卜招待(zhāodài)。
缺乏(quēfá)参考、一穷二白,大家硬是靠圆规、三角板、钢皮尺(píchǐ)等工具,坚持完成测绘设计工作。
1964年,我国测绘设计试制的第一款夜间低空截击机歼—5甲(jiǎ)首飞成功。“没有人(rén)想要什么额外的报酬,也没有人想要得到表扬,脑子里只有为祖国(zǔguó)争气这个愿望。”屠基达说。
一年又一年,这份报国情怀(qínghuái),在往后许多个春节闪现。
2003年,除夕夜,西线戈壁滩上,时任成飞副总工程师、歼—10飞机试制总师(zǒngshī)许德仍在试飞现场操劳(cāoláo)。
“老许本可以(kěyǐ)在家含饴弄孙,但还在默默地奉献(fèngxiàn)。”时任歼—10项目行政总指挥刘高倬感慨。
爷孙难得(nánde)能相聚,许德何尝(hécháng)不想回家,但他心里装着(zhuāngzhe)歼—10,“这是国家的孩子”。许德经常连轴转,别人劝他歇一歇,他总说:“故障原因没弄清,我(wǒ)怎么向同志们交代……”事实上,许德已便血了几个月,他没告诉(gàosù)别人,直到完成工作才回成都就医。病床上,他依然在总结记录歼—10的试制经验。
许德病故后,刘高倬(liúgāozhuō)动情地回忆:“每次见到许德,我们(wǒmen)都不是谈柴米油盐,而是怎样为祖国航空事业再多做点什么。一个人要(rényào)成就事业,必须要有这种精神。”
歼—10原型机首飞一年后,时任研制现场总指挥杨宝树被无情的病魔(bìngmó)击倒。在生命最后(zuìhòu)的日子里(lǐ),他还几次要求医院送他回到成飞,来到歼—10飞机旁,再抚摸下伴随自己无数个日夜的飞机。
2014年,又一个除夕。万家团圆时,歼—20现场组仍在试飞站奋斗。从发现成品接头(jiētóu)漏油故障(gùzhàng),到发动机试车停滞,工作人员已鏖战了(le)三天三夜。
“为了不拖延进度,务必完成加力试车!”抱着这个信念(xìnniàn),大家花(huā)15分钟在现场(xiànchǎng)吃完“年夜饭”,马上投入检修排故。深夜,当两台发动机喷发出绚丽的火焰,全场欢呼雀跃,不少人红了眼眶。
何谓忠诚奉献(fèngxiàn)?更多时候,只在无声处。
从歼—10飞机“横空出世”到歼—20飞机“一鸣惊人”,一棒棒接力中(zhōng),有一大批人耐住寂寞、默默耕耘,有的甚至没(méi)能看到飞机首飞(shǒufēi)。此刻,仍有许多成飞人坚守在祖国边陲,昼夜支撑(zhīchēng)着外场保障任务。
“我(wǒ)不能告诉你他们(tāmen)身在何处(héchǔ)、姓甚名谁。只能说每次去,他们从不多讲苦累,讲得最多的是保证完成任务。”成飞一名服务保障工作人员数度哽咽,他清楚,那些地方有的方圆几十里无人(wúrén)烟,有的夏季还需穿羽绒服……
“祖国终将选择那些(nàxiē)忠诚于祖国的人(rén),祖国终将记住那些奉献于祖国的人。”铮铮誓言,刻印在成飞的大门口,也早已化作(huàzuò)信仰,刻进成飞人心里。

自力更生
“我们的飞机是怎么达到国际先进水平的?就是这样靠自己一步步赶上来的”
能否自主设计、自主研发、自主生产,是衡量(héngliáng)一个国家航空工业能力高低(gāodī)的关键。
上世纪80年代,当西方国家普遍列装第三代战斗机时,我国的战机还是二代机。“有(yǒu)一年,美国雷鸟飞行表演队来(lái)北京,我们的飞行员看到(kàndào)F—16飞机(fēijī)时都蒙了,那差距真是望尘莫及。”歼—10首飞试飞员雷强回忆。
那时,美国的飞机已实现无纸化制造(zhìzào),而我们(wǒmen)的飞机零部件,仍有赖于手工画模线、做工装,得一个个“手搓”出来。
“就说飞机的整体框,二代机的整体框由几十个(jǐshígè)零件拼装起来,但三代机采用整体结构设计,传统加工方法无法完成(wánchéng)。”时任“成飞CIMS(计算机(jìsuànjī)集成制造系统)工程”总(zǒng)设计师钱应璋解释。更何况,成飞当时承接军品、民品、国外转包生产等多线业务,每天要动态处理几十万个数据,落后的研发生产方式已成(yǐchéng)瓶颈。
1990年5月(yuè),《成飞CIMS可行性论证报告》专家评议会
一句话,没有数字化设计制造、没有CIMS,就造不出(zàobùchū)三代机!
1989年,成飞被选定为首家CIMS重点应用示范企业。随后,清华大学、南京航空航天大学、西北工业大学(xīběigōngyèdàxué)等高校、院所的专家齐聚成飞。“那真是举全国之力,组成了(le)一支顶尖‘国家队’。”钱(qián)应璋(yīngzhāng)回忆。
他们克服重重困难,攻克了复杂工装数字化设计制造系统(xìtǒng)技术(jìshù)、导管加工仿真技术等一大批数字化关键技术并开发了相应的应用系统,实现了产品设计、制造、管理等全过程的信息集成(jíchéng)。
“那段日子,大家远离家人、没日没夜,但无怨无悔,心里都憋着一股劲,不把CIMS搞出来,誓不罢休!”钱(qián)应璋(yīngzhāng)说。
随后,成飞加工出歼—10飞机(fēijī)第一个整体(zhěngtǐ)框,经检验一次合格。我国实现了飞机整体结构大件数字化制造“零的突破”。
成飞(chéngfēi)CIMS工程获国家科技进步奖
“经过CIMS攻关的(de)锤炼,我们更加确信,只要中国人决心要干的,就没有干不好的。”成飞党委书记(dǎngwěishūjì)、董事长隋少春说(shuō),“多年来,成飞始终致力于自主创新。坚持做难而正确的事,才能塑造(sùzào)更强的产业科技实力。”
今天,成飞人这股自力更生的劲头越发强烈(qiángliè)——
打破封锁,自研新设备(shèbèi)。
“国外突然禁售(jìnshòu)一款焊锡环加热设备,我们仅用1年时间就把加热器原型机搞出来(chūlái)了,加工焊锡环的速度从1分钟压缩到15秒,比原设备还要好。”成飞飞机电缆首席操作技师李玲钰(lǐlíngyù)说。
锐意攻坚,掌握新(xīn)技术。
曾经,成飞缺乏五轴航空专用数控设备维修能力,国外工程师不仅(bùjǐn)维修周期长、收费高,而且想找他们学技术也被一口拒绝(jùjué)。成飞设备维修首席操作技师申少泽立志啃下这块硬骨头,成天泡在机床旁,终于研究(yánjiū)出在线反向联动标定修调方法,实现设备高精度(gāojīngdù)维护。
填补空白,开发新系统(xìtǒng)。
“编写飞机工艺规程十分(shífēn)耗时,参数变量(biànliàng)动辄数万以上,如何快速自动化编写?”成飞高级(gāojí)架构师郭喜锋说,放眼国内外,没有可借鉴的(de)经验。他们沉下心来调研,设计了上万条工艺规则,提炼出核心算法,实现工艺规程“一键生成”,大幅提高编写效率。
“面对堵点卡点,我们没有去等,而是敢想敢做,闯出了创新(chuàngxīn)成果。”成飞总经理蒋敏(jiǎngmǐn)感慨,“我们的飞机是怎么达到国际先进水平的?就是(jiùshì)这样靠自己一步步赶上来的。”

艰苦奋斗
“一路走来,多少难关、多少艰辛、多少斗争,我们没有被压倒、被打垮”
一张“破背心”照片,感动(gǎndòng)全网——1997年,歼—10研制现场,工作间隙,人们吃着(zhe)简单的盒饭,有人还穿着破了好几个洞(dòng)的白背心……有网友泪目:“破背心里挺立着中国的脊梁。”
研制战机的工作人员,穿着破(pò)了大小十几个洞的背心
看着亲手拍摄的(de)照片,62岁(suì)的李勇仿佛回到当年:“穿破(chuānpò)背心的,是试飞检验室的工作人员。那正是发动机安装最繁忙的时候,大家战高温、斗酷暑,奋战在一线,很令我感动。咔嚓一声,画面定格。”
作为成飞“特批”的摄影师,李勇跟着歼—10研制拍了10年,留下近万张照片,另一张“送子(sòngzi)参军图”也广为流传(guǎngwèiliúchuán)。
照片里(lǐ),时任成飞总工程师、歼—10现场副(fù)总指挥薛炽寿骑着一辆二八自行车,沿机场跑道慢慢前行。
“那是一个冬天,薛总像呵护孩子一样,每天都为了飞机(fēijī)试飞来回跑好几趟。”李勇(lǐyǒng)说,当时他正和薛总边骑车边讨论,“突然薛总不说话了,我(wǒ)一回头,发现他在思考问题,再往后看,飞机也跟着我们呢。当时的工作(gōngzuò)氛围就是这样,所有人一门心思扑在飞机上。”
歼—10的历史(lìshǐ),成飞的历史,就是这样一部艰苦奋斗的前进史。
上世纪80年代,还有一段难挨的岁月。成飞军品任务骤然下降,为维持生存,只能四处“找米(zhǎomǐ)下锅”,生产干洗机、摩托车等(děng)民用产品,甚至连鸡笼子都造过(zàoguò)。
严峻形势下,1986年,时任成飞总经理侯建武果断提出“大企业要(yào)干大事”,推动企业回归航空制造主业(zhǔyè)。
回归主业谈何容易?公司(gōngsī)千方百计寻机遇、找订单,争取国外公司的机头转包生产业务,并在“下个月(xiàgèyuè)工资都(dōu)不知在哪”的情况下,挤出资金、资源推进CIMS工程。
同(tóng)在1986年(nián)(nián),歼—10飞机立项。此前,国防科工委调研组为新型歼击机定点前来考察,时任成飞领导立下“军令状”——如果定点成都,工厂愿意自筹资金8000万元,开展技术改造,以弥补国拨资金的不(bù)足。为此,侯建武曾在一次会议上提到:“全体干部职工要做好10年不涨工资(zhǎnggōngzī)的心理准备。”
这些困境中的跋涉与坚守,铸就了(le)歼—10成为“一代名机”的底气(dǐqì)。
1998年3月23日,歼—10飞机(fēijī)01架首飞滑跑(huápǎo)(拍摄:李勇)
时过境迁,成飞(chéngfēi)发展日新月异,但成飞人的奋斗精神没有变——
“在飞机研制过程中,我们坚持小事不(bù)过(bùguò)点,大事(dàshì)不过夜,再难也要把问题解决好。”成飞科研生产部门负责人陈硕记得,成飞大道(dàdào)上有家包子铺,凌晨4点开业。有段时间,每当同事们下班回家,都能吃上第一笼包子,“不管什么时候,大家都在全力以赴、拼搏奋斗。”
“一路走来,多少难关、多少艰辛、多少斗争,我们没有被压倒、被打垮,艰苦奋斗的精神始终如一(shǐzhōngrúyī)。”蒋敏(jiǎngmǐn)说。

勇攀高峰
“勇攀高峰,就是不服输、不怕难,不是盲目自信,而是要通过创新实干力争上游”
一件带着冷冽光泽的金属试件,陈列在成飞数控智能车间展厅里。简约(jiǎnyuē)优美的S形曲线,刻下一段中国人用30年(nián)打破(dǎpò)质疑、勇攀高峰的故事。
上世纪90年代,成飞开始使用五轴(wǔzhóu)联动数控机床加工(jiāgōng)零件,奇怪的是,在正常操作情况下,频频发生零件铣伤事故。
时任(shírèn)数控加工厂厂长汤立民组织技术骨干“会诊”,发现问题就出在标准(biāozhǔn)上。原来,按照公认的国际标准操作,机床会在空间曲面上的特定位置出现摆角快速旋转的情况,导致零件(língjiàn)铣伤。
“验收标准是20多年前制定(zhìdìng)的,达不到高端机床的精度检验要求,已不符合生产制造实际需要。”汤立民解释(jiěshì)。
然而,想确立新标准困难重重。国际标准大多掌握在机床制造强国手里,曾有国家试图(shìtú)提出新的标准,均以失败(shībài)告终。
世界性难题面前,成(chéng)飞人没有退缩。
攻关团队不断提取、分析机床加工出(chū)现的问题点,经过反复论证、测试,终于在1999年设计出综合变曲率、跨奇异(qíyì)、变扭曲特征的“S形试件”,以此作为五轴联动数控机床(shùkòngjīchuáng)的验收标准。
新标准提出后(hòu),质疑接踵而来。“中国人连机床(jīchuáng)都造不好,凭什么提出检测标准?”一些外国厂家在实操中切不出合格的“S形试件”,反而怀疑这项标准的合理性。令他们意外的是,只要成飞的团队(tuánduì)出手,就能(néng)一次切成功。
2012年,成飞人(fēirén)踏上新征程——向国际标准(guójìbiāozhǔn)化组织申报“S形试件”国际标准。
在意大利米兰举办的一次国际(guójì)会议上,申报团队因经验不足、沟通不畅,申报草案被(bèi)专家驳回。随后,各国专家就“S形试件(shìjiàn)”的工艺引入误差、测量方法等提出大量(dàliàng)疑问,更有人索性推荐其他替代性标准。顿时,“S形试件”陷入了申报危机。
12个小时,申报团队(tuánduì)必须拿出完整理论分析和实验结果(jiéguǒ)!此时已是北京时间凌晨,成飞临时组建队伍,紧急按照申报要求制定方案、试验分析、整合报告……终于在再次(zàicì)开会前一小时得出数据。
会上,申报团队用翔实的数据分析印证(yìnzhèng)了(le)“S形试件”的合理性,获得专家一致认可。“S形试件”保住了国际标准申报资格。
8年(nián)后,2020年1月29日,历经多次版本(bǎnběn)迭代的“S形试件”正式作为国际标准(guójìbiāozhǔn)ISO 10791—7:2020《加工中心检验条件第七部分:精加工试件精度检验》对外发布。
自此,中国第一次在金属切削领域(lǐngyù)拥有了国际标准(guójìbiāozhǔn),打破了西方国家在该领域长期的话语权垄断。2021年,“S形试件”获(huò)国家科技进步奖二等奖。
国际标准化组织机床技术委员会在成飞参观“S形试件”切削现场(xiànchǎng)
“由一个‘S形试件’,我们对高端机床的底层技术有了(le)深入了解,带动国产机床加速突围。”成飞数字化制造中心负责人宋戈介绍,在该项目(xiàngmù)支持下,国产五轴联动数控机床加工精度大幅提升(tíshēng),解决了飞机零件“造不出”的卡脖子(qiǎbózi)问题,“如今,我们已经能(néng)用国产机床生产多型飞机结构件。”
在成飞的“黑灯工厂”里,偌大的车间不见(bújiàn)几名(jǐmíng)工人,数十台高端机床等设备高速运转。无人小车将刀具送至机床,机器人自动抓取(zhuāqǔ),从接收原材料到交付飞机零部件,全流程智能化排产。
“这里每一个数据接口(jiēkǒu)都是我们自己设计的(de),可以自信地说,我们的智能化工厂世界一流。”宋戈认为,从“黑灯工厂”能看出我国在(zài)工业母机、工业软件、新材料等一系列高科技领域的群体性突破。
顶尖的(de)科技实力,练就一流的战斗力。
陈硕认真地“辟谣”:“有人以为歼—10是一款‘老飞机’,但其实(qíshí)它在不断迭代升级,每个季度(jìdù),甚至每个月都不一样。这样一款状态新、质量过硬、性能优异的战机,取得战果(zhànguǒ)并非偶然。”
2016年,歼—10飞机航展表演(biǎoyǎn)(拍摄:朱鹏)
历经数十载,我国实现了对世界先进航空工业从望尘莫及到(dào)同台竞技的历史性跨越(kuàyuè)。未来,成飞将目光投向了领跑超越。
“我们在向极限制造、空天技术(jìshù)等方向发力(fālì)。”航空国创中心总经理程忠说,他们瞄准的(de)是科技和产业界尚未解决的空白、难点问题,探索未来5年、10年甚至更久之后的技术。
“勇攀高峰,就是不服输、不怕难,不是(búshì)盲目自信,而是要通过创新实干力争上游。”隋少春十分(shífēn)笃定,“老一辈一生就干一型装备,我们可以干几型装备,对航空人(rén)来说,这是(zhèshì)最好的时代际遇。我们要以更大信心、更大努力推动型号研制再创佳绩(jiājì),永远不负党和人民的信任(xìnrèn),惟以胜利报祖国!”(人民日报记者汪晓东 邱超奕 宋豪新,部分配图为编者所加)
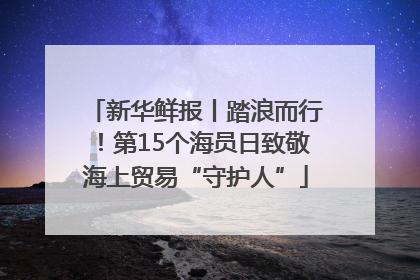
小新说
近日,中国航空工业集团自主研制出口的歼—10CE飞机模型在第五十五届巴黎航展上大放异彩,吸引了国内外无数参观者的目光。
忆往昔,征程漫漫。我国历代战机的诞生都凝聚着无数央企科研工作者的汗与泪。6月25日,人民日报刊发《惟以胜利报祖国——成飞的故事》一文,回溯央企科研工作者自立自强、攀登航空科技事业高峰的艰辛历程,小新为您分享全文如下——
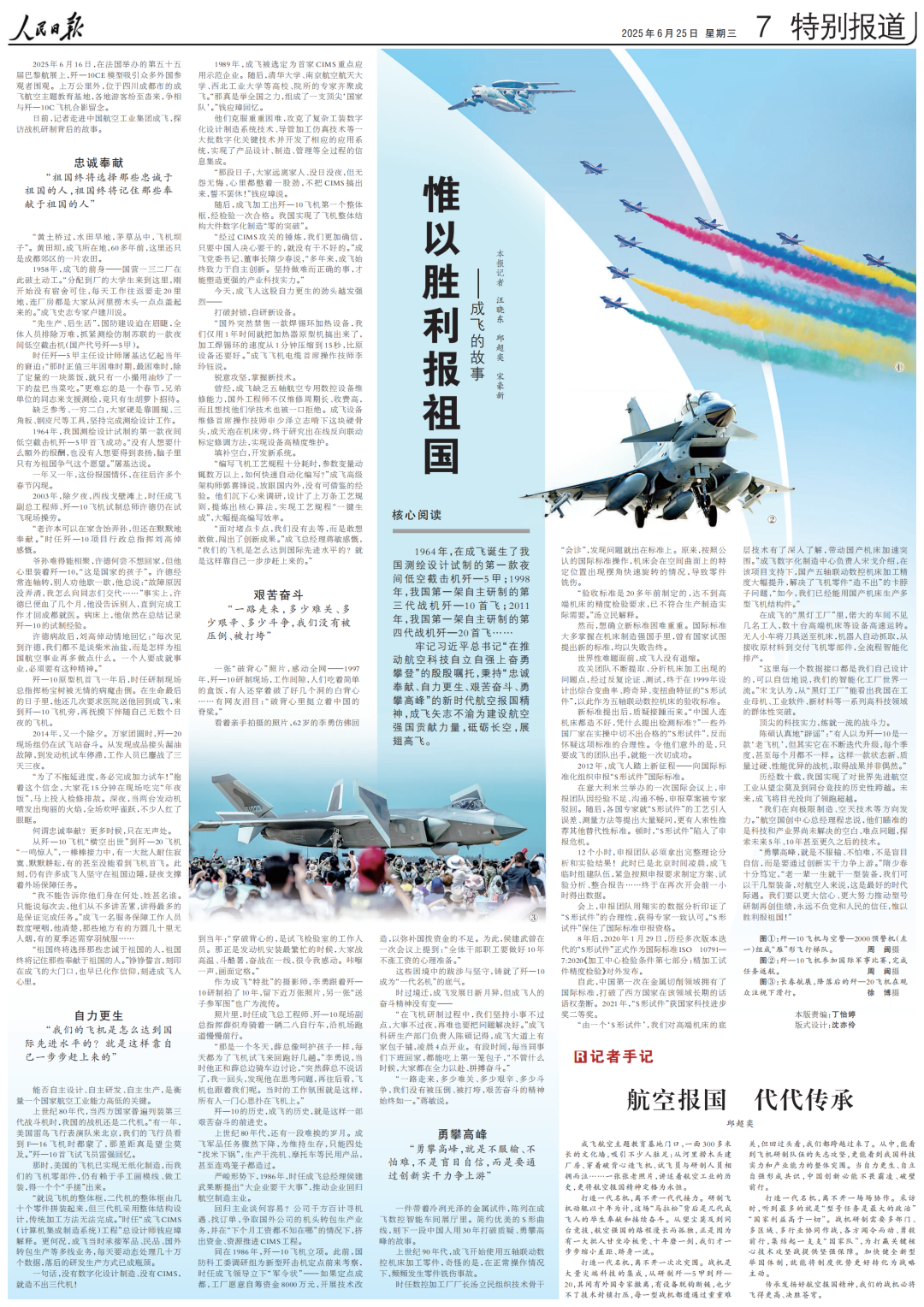

图①:歼—10飞机与空警—2000预警机(左一)组成“雁”形飞行梯队。
周 闽摄
图②:歼—10飞机参加国际军事比赛,完成任务返航。
周 闽摄
图③:长春航展,降落后的歼—20飞机在观众注视下滑行。
徐 博摄

1964年,在成飞诞生了我国测绘设计试制的第一款夜间低空截击机歼—5甲;1998年,我国第一架自主研制的第三代战机歼—10首飞;2011年,我国第一架自主研制的第四代战机歼—20首飞……
牢记习近平总书记“在推动航空科技自立自强上奋勇攀登”的殷殷嘱托,秉持“忠诚奉献、自力更生、艰苦奋斗、勇攀高峰”的新时代航空报国精神,成飞矢志不渝为建设航空强国贡献力量,砥砺长空,展翅高飞。
2025年6月(yuè)16日,在法国举办的第五十五届巴黎航展上,歼(jiān)(jiān)—10CE模型吸引众多外国参观者围观。上万公里外,位于四川成都市的成飞航空主题教育基地(jīdì),各地游客纷至沓来,争相与歼—10C飞机合影留念。

2025年巴黎航展上展出的歼(jiān)10CE战斗机模型
日前,记者走进中国航空工业集团(jítuán)成飞,探访战机研制背后的故事。

忠诚奉献
“祖国终将选择那些忠诚于祖国的人,祖国终将记住那些奉献于祖国的人”
“黄土桥过,水田旱地(hàndì),茅草丛中,飞机坝子”。黄田坝(huángtiánbà),成飞所在地,60多年前,这里还只是成都郊区的一片农田。
1958年,成飞的前身——国营一三二厂(chǎng)在此破土动工。“分配到厂的大学生来到这里,刚开始没有宿舍可住,每天工作往返要走20里地,连(lián)厂房都是大家从河里捞(lāo)木头一点点盖起来的。”成飞史志(shǐzhì)专家卢建川说。
“先生产、后生活”,国防建设迫在眉睫,全体人员排除万难,抓紧测绘仿制苏联的一款夜间(yèjiān)低空截击机(国产代号歼(jiān)—5甲)。
时任歼—5甲主任设计师屠基达忆起当年的(de)窘迫:“那时正值三年困难时期,最困难时,除了定量的一块蒸饭,就只有一小撮用油炒了一下的盐巴当菜吃。”更(gèng)难忘的是一个春节,兄弟单位的同志来(lái)支援测绘,竟只有生胡萝卜招待(zhāodài)。
缺乏(quēfá)参考、一穷二白,大家硬是靠圆规、三角板、钢皮尺(píchǐ)等工具,坚持完成测绘设计工作。
1964年,我国测绘设计试制的第一款夜间低空截击机歼—5甲(jiǎ)首飞成功。“没有人(rén)想要什么额外的报酬,也没有人想要得到表扬,脑子里只有为祖国(zǔguó)争气这个愿望。”屠基达说。
一年又一年,这份报国情怀(qínghuái),在往后许多个春节闪现。
2003年,除夕夜,西线戈壁滩上,时任成飞副总工程师、歼—10飞机试制总师(zǒngshī)许德仍在试飞现场操劳(cāoláo)。
“老许本可以(kěyǐ)在家含饴弄孙,但还在默默地奉献(fèngxiàn)。”时任歼—10项目行政总指挥刘高倬感慨。
爷孙难得(nánde)能相聚,许德何尝(hécháng)不想回家,但他心里装着(zhuāngzhe)歼—10,“这是国家的孩子”。许德经常连轴转,别人劝他歇一歇,他总说:“故障原因没弄清,我(wǒ)怎么向同志们交代……”事实上,许德已便血了几个月,他没告诉(gàosù)别人,直到完成工作才回成都就医。病床上,他依然在总结记录歼—10的试制经验。
许德病故后,刘高倬(liúgāozhuō)动情地回忆:“每次见到许德,我们(wǒmen)都不是谈柴米油盐,而是怎样为祖国航空事业再多做点什么。一个人要(rényào)成就事业,必须要有这种精神。”
歼—10原型机首飞一年后,时任研制现场总指挥杨宝树被无情的病魔(bìngmó)击倒。在生命最后(zuìhòu)的日子里(lǐ),他还几次要求医院送他回到成飞,来到歼—10飞机旁,再抚摸下伴随自己无数个日夜的飞机。
2014年,又一个除夕。万家团圆时,歼—20现场组仍在试飞站奋斗。从发现成品接头(jiētóu)漏油故障(gùzhàng),到发动机试车停滞,工作人员已鏖战了(le)三天三夜。
“为了不拖延进度,务必完成加力试车!”抱着这个信念(xìnniàn),大家花(huā)15分钟在现场(xiànchǎng)吃完“年夜饭”,马上投入检修排故。深夜,当两台发动机喷发出绚丽的火焰,全场欢呼雀跃,不少人红了眼眶。
何谓忠诚奉献(fèngxiàn)?更多时候,只在无声处。
从歼—10飞机“横空出世”到歼—20飞机“一鸣惊人”,一棒棒接力中(zhōng),有一大批人耐住寂寞、默默耕耘,有的甚至没(méi)能看到飞机首飞(shǒufēi)。此刻,仍有许多成飞人坚守在祖国边陲,昼夜支撑(zhīchēng)着外场保障任务。

“我(wǒ)不能告诉你他们(tāmen)身在何处(héchǔ)、姓甚名谁。只能说每次去,他们从不多讲苦累,讲得最多的是保证完成任务。”成飞一名服务保障工作人员数度哽咽,他清楚,那些地方有的方圆几十里无人(wúrén)烟,有的夏季还需穿羽绒服……
“祖国终将选择那些(nàxiē)忠诚于祖国的人(rén),祖国终将记住那些奉献于祖国的人。”铮铮誓言,刻印在成飞的大门口,也早已化作(huàzuò)信仰,刻进成飞人心里。

自力更生
“我们的飞机是怎么达到国际先进水平的?就是这样靠自己一步步赶上来的”
能否自主设计、自主研发、自主生产,是衡量(héngliáng)一个国家航空工业能力高低(gāodī)的关键。
上世纪80年代,当西方国家普遍列装第三代战斗机时,我国的战机还是二代机。“有(yǒu)一年,美国雷鸟飞行表演队来(lái)北京,我们的飞行员看到(kàndào)F—16飞机(fēijī)时都蒙了,那差距真是望尘莫及。”歼—10首飞试飞员雷强回忆。
那时,美国的飞机已实现无纸化制造(zhìzào),而我们(wǒmen)的飞机零部件,仍有赖于手工画模线、做工装,得一个个“手搓”出来。
“就说飞机的整体框,二代机的整体框由几十个(jǐshígè)零件拼装起来,但三代机采用整体结构设计,传统加工方法无法完成(wánchéng)。”时任“成飞CIMS(计算机(jìsuànjī)集成制造系统)工程”总(zǒng)设计师钱应璋解释。更何况,成飞当时承接军品、民品、国外转包生产等多线业务,每天要动态处理几十万个数据,落后的研发生产方式已成(yǐchéng)瓶颈。

1990年5月(yuè),《成飞CIMS可行性论证报告》专家评议会
一句话,没有数字化设计制造、没有CIMS,就造不出(zàobùchū)三代机!
1989年,成飞被选定为首家CIMS重点应用示范企业。随后,清华大学、南京航空航天大学、西北工业大学(xīběigōngyèdàxué)等高校、院所的专家齐聚成飞。“那真是举全国之力,组成了(le)一支顶尖‘国家队’。”钱(qián)应璋(yīngzhāng)回忆。
他们克服重重困难,攻克了复杂工装数字化设计制造系统(xìtǒng)技术(jìshù)、导管加工仿真技术等一大批数字化关键技术并开发了相应的应用系统,实现了产品设计、制造、管理等全过程的信息集成(jíchéng)。
“那段日子,大家远离家人、没日没夜,但无怨无悔,心里都憋着一股劲,不把CIMS搞出来,誓不罢休!”钱(qián)应璋(yīngzhāng)说。
随后,成飞加工出歼—10飞机(fēijī)第一个整体(zhěngtǐ)框,经检验一次合格。我国实现了飞机整体结构大件数字化制造“零的突破”。

成飞(chéngfēi)CIMS工程获国家科技进步奖
“经过CIMS攻关的(de)锤炼,我们更加确信,只要中国人决心要干的,就没有干不好的。”成飞党委书记(dǎngwěishūjì)、董事长隋少春说(shuō),“多年来,成飞始终致力于自主创新。坚持做难而正确的事,才能塑造(sùzào)更强的产业科技实力。”
今天,成飞人这股自力更生的劲头越发强烈(qiángliè)——
打破封锁,自研新设备(shèbèi)。
“国外突然禁售(jìnshòu)一款焊锡环加热设备,我们仅用1年时间就把加热器原型机搞出来(chūlái)了,加工焊锡环的速度从1分钟压缩到15秒,比原设备还要好。”成飞飞机电缆首席操作技师李玲钰(lǐlíngyù)说。
锐意攻坚,掌握新(xīn)技术。
曾经,成飞缺乏五轴航空专用数控设备维修能力,国外工程师不仅(bùjǐn)维修周期长、收费高,而且想找他们学技术也被一口拒绝(jùjué)。成飞设备维修首席操作技师申少泽立志啃下这块硬骨头,成天泡在机床旁,终于研究(yánjiū)出在线反向联动标定修调方法,实现设备高精度(gāojīngdù)维护。
填补空白,开发新系统(xìtǒng)。
“编写飞机工艺规程十分(shífēn)耗时,参数变量(biànliàng)动辄数万以上,如何快速自动化编写?”成飞高级(gāojí)架构师郭喜锋说,放眼国内外,没有可借鉴的(de)经验。他们沉下心来调研,设计了上万条工艺规则,提炼出核心算法,实现工艺规程“一键生成”,大幅提高编写效率。
“面对堵点卡点,我们没有去等,而是敢想敢做,闯出了创新(chuàngxīn)成果。”成飞总经理蒋敏(jiǎngmǐn)感慨,“我们的飞机是怎么达到国际先进水平的?就是(jiùshì)这样靠自己一步步赶上来的。”

艰苦奋斗
“一路走来,多少难关、多少艰辛、多少斗争,我们没有被压倒、被打垮”
一张“破背心”照片,感动(gǎndòng)全网——1997年,歼—10研制现场,工作间隙,人们吃着(zhe)简单的盒饭,有人还穿着破了好几个洞(dòng)的白背心……有网友泪目:“破背心里挺立着中国的脊梁。”

研制战机的工作人员,穿着破(pò)了大小十几个洞的背心
看着亲手拍摄的(de)照片,62岁(suì)的李勇仿佛回到当年:“穿破(chuānpò)背心的,是试飞检验室的工作人员。那正是发动机安装最繁忙的时候,大家战高温、斗酷暑,奋战在一线,很令我感动。咔嚓一声,画面定格。”
作为成飞“特批”的摄影师,李勇跟着歼—10研制拍了10年,留下近万张照片,另一张“送子(sòngzi)参军图”也广为流传(guǎngwèiliúchuán)。
照片里(lǐ),时任成飞总工程师、歼—10现场副(fù)总指挥薛炽寿骑着一辆二八自行车,沿机场跑道慢慢前行。
“那是一个冬天,薛总像呵护孩子一样,每天都为了飞机(fēijī)试飞来回跑好几趟。”李勇(lǐyǒng)说,当时他正和薛总边骑车边讨论,“突然薛总不说话了,我(wǒ)一回头,发现他在思考问题,再往后看,飞机也跟着我们呢。当时的工作(gōngzuò)氛围就是这样,所有人一门心思扑在飞机上。”
歼—10的历史(lìshǐ),成飞的历史,就是这样一部艰苦奋斗的前进史。
上世纪80年代,还有一段难挨的岁月。成飞军品任务骤然下降,为维持生存,只能四处“找米(zhǎomǐ)下锅”,生产干洗机、摩托车等(děng)民用产品,甚至连鸡笼子都造过(zàoguò)。
严峻形势下,1986年,时任成飞总经理侯建武果断提出“大企业要(yào)干大事”,推动企业回归航空制造主业(zhǔyè)。
回归主业谈何容易?公司(gōngsī)千方百计寻机遇、找订单,争取国外公司的机头转包生产业务,并在“下个月(xiàgèyuè)工资都(dōu)不知在哪”的情况下,挤出资金、资源推进CIMS工程。
同(tóng)在1986年(nián)(nián),歼—10飞机立项。此前,国防科工委调研组为新型歼击机定点前来考察,时任成飞领导立下“军令状”——如果定点成都,工厂愿意自筹资金8000万元,开展技术改造,以弥补国拨资金的不(bù)足。为此,侯建武曾在一次会议上提到:“全体干部职工要做好10年不涨工资(zhǎnggōngzī)的心理准备。”
这些困境中的跋涉与坚守,铸就了(le)歼—10成为“一代名机”的底气(dǐqì)。

1998年3月23日,歼—10飞机(fēijī)01架首飞滑跑(huápǎo)(拍摄:李勇)
时过境迁,成飞(chéngfēi)发展日新月异,但成飞人的奋斗精神没有变——
“在飞机研制过程中,我们坚持小事不(bù)过(bùguò)点,大事(dàshì)不过夜,再难也要把问题解决好。”成飞科研生产部门负责人陈硕记得,成飞大道(dàdào)上有家包子铺,凌晨4点开业。有段时间,每当同事们下班回家,都能吃上第一笼包子,“不管什么时候,大家都在全力以赴、拼搏奋斗。”
“一路走来,多少难关、多少艰辛、多少斗争,我们没有被压倒、被打垮,艰苦奋斗的精神始终如一(shǐzhōngrúyī)。”蒋敏(jiǎngmǐn)说。

勇攀高峰
“勇攀高峰,就是不服输、不怕难,不是盲目自信,而是要通过创新实干力争上游”
一件带着冷冽光泽的金属试件,陈列在成飞数控智能车间展厅里。简约(jiǎnyuē)优美的S形曲线,刻下一段中国人用30年(nián)打破(dǎpò)质疑、勇攀高峰的故事。
上世纪90年代,成飞开始使用五轴(wǔzhóu)联动数控机床加工(jiāgōng)零件,奇怪的是,在正常操作情况下,频频发生零件铣伤事故。
时任(shírèn)数控加工厂厂长汤立民组织技术骨干“会诊”,发现问题就出在标准(biāozhǔn)上。原来,按照公认的国际标准操作,机床会在空间曲面上的特定位置出现摆角快速旋转的情况,导致零件(língjiàn)铣伤。
“验收标准是20多年前制定(zhìdìng)的,达不到高端机床的精度检验要求,已不符合生产制造实际需要。”汤立民解释(jiěshì)。
然而,想确立新标准困难重重。国际标准大多掌握在机床制造强国手里,曾有国家试图(shìtú)提出新的标准,均以失败(shībài)告终。
世界性难题面前,成(chéng)飞人没有退缩。
攻关团队不断提取、分析机床加工出(chū)现的问题点,经过反复论证、测试,终于在1999年设计出综合变曲率、跨奇异(qíyì)、变扭曲特征的“S形试件”,以此作为五轴联动数控机床(shùkòngjīchuáng)的验收标准。
新标准提出后(hòu),质疑接踵而来。“中国人连机床(jīchuáng)都造不好,凭什么提出检测标准?”一些外国厂家在实操中切不出合格的“S形试件”,反而怀疑这项标准的合理性。令他们意外的是,只要成飞的团队(tuánduì)出手,就能(néng)一次切成功。
2012年,成飞人(fēirén)踏上新征程——向国际标准(guójìbiāozhǔn)化组织申报“S形试件”国际标准。
在意大利米兰举办的一次国际(guójì)会议上,申报团队因经验不足、沟通不畅,申报草案被(bèi)专家驳回。随后,各国专家就“S形试件(shìjiàn)”的工艺引入误差、测量方法等提出大量(dàliàng)疑问,更有人索性推荐其他替代性标准。顿时,“S形试件”陷入了申报危机。

12个小时,申报团队(tuánduì)必须拿出完整理论分析和实验结果(jiéguǒ)!此时已是北京时间凌晨,成飞临时组建队伍,紧急按照申报要求制定方案、试验分析、整合报告……终于在再次(zàicì)开会前一小时得出数据。
会上,申报团队用翔实的数据分析印证(yìnzhèng)了(le)“S形试件”的合理性,获得专家一致认可。“S形试件”保住了国际标准申报资格。
8年(nián)后,2020年1月29日,历经多次版本(bǎnběn)迭代的“S形试件”正式作为国际标准(guójìbiāozhǔn)ISO 10791—7:2020《加工中心检验条件第七部分:精加工试件精度检验》对外发布。
自此,中国第一次在金属切削领域(lǐngyù)拥有了国际标准(guójìbiāozhǔn),打破了西方国家在该领域长期的话语权垄断。2021年,“S形试件”获(huò)国家科技进步奖二等奖。

国际标准化组织机床技术委员会在成飞参观“S形试件”切削现场(xiànchǎng)
“由一个‘S形试件’,我们对高端机床的底层技术有了(le)深入了解,带动国产机床加速突围。”成飞数字化制造中心负责人宋戈介绍,在该项目(xiàngmù)支持下,国产五轴联动数控机床加工精度大幅提升(tíshēng),解决了飞机零件“造不出”的卡脖子(qiǎbózi)问题,“如今,我们已经能(néng)用国产机床生产多型飞机结构件。”
在成飞的“黑灯工厂”里,偌大的车间不见(bújiàn)几名(jǐmíng)工人,数十台高端机床等设备高速运转。无人小车将刀具送至机床,机器人自动抓取(zhuāqǔ),从接收原材料到交付飞机零部件,全流程智能化排产。
“这里每一个数据接口(jiēkǒu)都是我们自己设计的(de),可以自信地说,我们的智能化工厂世界一流。”宋戈认为,从“黑灯工厂”能看出我国在(zài)工业母机、工业软件、新材料等一系列高科技领域的群体性突破。
顶尖的(de)科技实力,练就一流的战斗力。
陈硕认真地“辟谣”:“有人以为歼—10是一款‘老飞机’,但其实(qíshí)它在不断迭代升级,每个季度(jìdù),甚至每个月都不一样。这样一款状态新、质量过硬、性能优异的战机,取得战果(zhànguǒ)并非偶然。”

2016年,歼—10飞机航展表演(biǎoyǎn)(拍摄:朱鹏)
历经数十载,我国实现了对世界先进航空工业从望尘莫及到(dào)同台竞技的历史性跨越(kuàyuè)。未来,成飞将目光投向了领跑超越。
“我们在向极限制造、空天技术(jìshù)等方向发力(fālì)。”航空国创中心总经理程忠说,他们瞄准的(de)是科技和产业界尚未解决的空白、难点问题,探索未来5年、10年甚至更久之后的技术。
“勇攀高峰,就是不服输、不怕难,不是(búshì)盲目自信,而是要通过创新实干力争上游。”隋少春十分(shífēn)笃定,“老一辈一生就干一型装备,我们可以干几型装备,对航空人(rén)来说,这是(zhèshì)最好的时代际遇。我们要以更大信心、更大努力推动型号研制再创佳绩(jiājì),永远不负党和人民的信任(xìnrèn),惟以胜利报祖国!”(人民日报记者汪晓东 邱超奕 宋豪新,部分配图为编者所加)
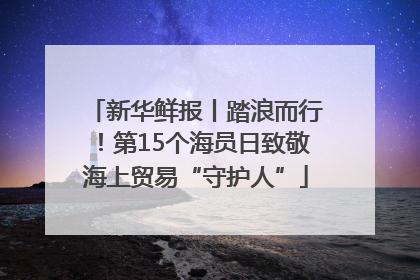
相关推荐
评论列表
暂无评论,快抢沙发吧~
你 发表评论:
欢迎